
“Cold” alignment of rotation machines
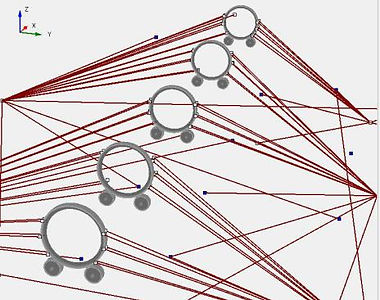

Locational cold alignment of rotation machines is based on high-accuracy laser measurements made by total station. The measurements are carried out in characteristic sections of the object and allow to determine geometrical parameters of the machine and its elements with high accuracy (accuracy 1 mm).
TECHNICAL REPORT on kinematic location alignment of rotary furnace №6 OOO “Iskitimcement


Laser measurement data can determine geometrical parameters of the machine elements both in distant measurement and in contact measurement. With high accuracy are determined:
· Geometrical centres of rolls, bands, shell sections;
· Directions of geometrical axes of elements in space;
· Radiuses and coning of elements;
· Straightness of machine axis in horizontal and vertical sections.
These data allow to estimate the form of objects, to build graphs of roll position in relation to kiln axis in horizontal and vertical sections, to calculate distances between centres and central angles. This information is enough to make decision about axis correction of the machine and its elements, repairing or replacement of rolls and bands.
Laser measurement by total station gives possibility to determine mutual special arrangement of shafts, gears, bearings etc. It lets perform analysis of mutual arrangement of gear rings and gear ring pinions, gear ring pinions and gear case shaft in horizontal and vertical sections.
In comparison with other technologies this technology of “cold” alignment allows to determine shell curve in any spot with necessary details in order to perform calculations for shell correction.
“Hot” alignment of rotation machines
“Hot” alignment of rotation machines is based on distant laser measurements of total station and performed without machine shutdown in usual operation condition. Measurements are performed only remotely, which excludes contact of surveyor with the machine warmed up to high temperature. For taking into account nonuniform rotation of the kiln there is a device for synchronization of kiln velocity rotation with geodetic measurements. Measurements are performed on-line by geodetic complex “Vizir 3D”, which determines not only geometrical but also kinematic parameters of the object .
The measurements are performed in the same way as in cold alignment by total station on the sections of the object, and the time of each measurement is recorded. The measurements results are processed according to the patented method right after the measurements have been completed. The informativity of “hot” alignment is much higher, than of other methods as the number of measurements is much higher. Hot alignment determines geometrical parameters:
· Geometrical centres of rolls, bands, shell sections;
· Directions of geometrical axes of elements in space;
· Radiuses and coning and form of elements;
· Straightness of machine axis in horizontal and vertical sections.
Kinematic parameters:
· Mismatching geometrical and rotation centres;
· Axial and radial beating of machine elements.







Измерение роликов при холодной выверке
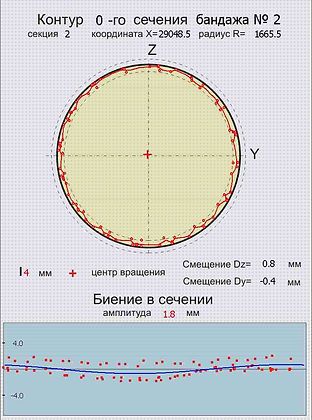
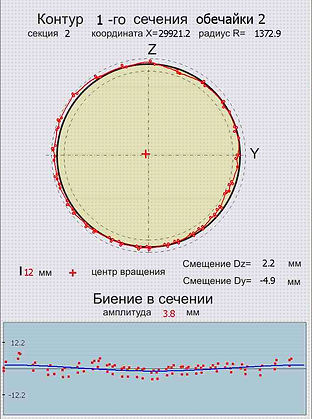



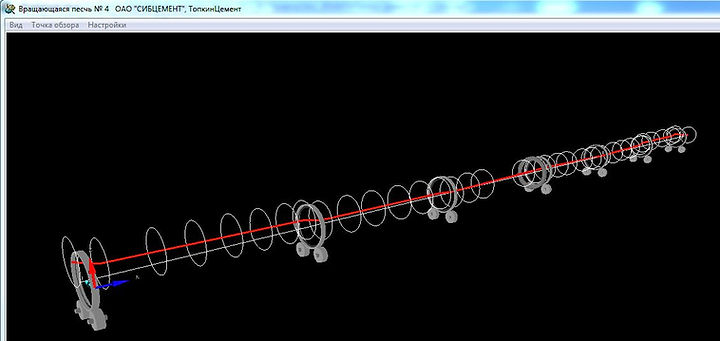
Extra information is available from the authors of technology and program complex:
Mogil'ny Sergej Georgievich, E-mail: mogilnysg@mail.ru
Sholomickij Andrej Arkad'evich, E-mail: sholomitskij@mail.ru tel: +7 913 373 07 51
RK № 8 alignment report
Patent № 2650418 "Method of high-accuracy determination of surface and axes parameters in rotation machines"